Neyveli Uttar Pradesh Power Ltd achieves major milestone
Synchronises Unit-1 of Supercritical Thermal Power Plant with the 765 KV grid
image for illustrative purpose
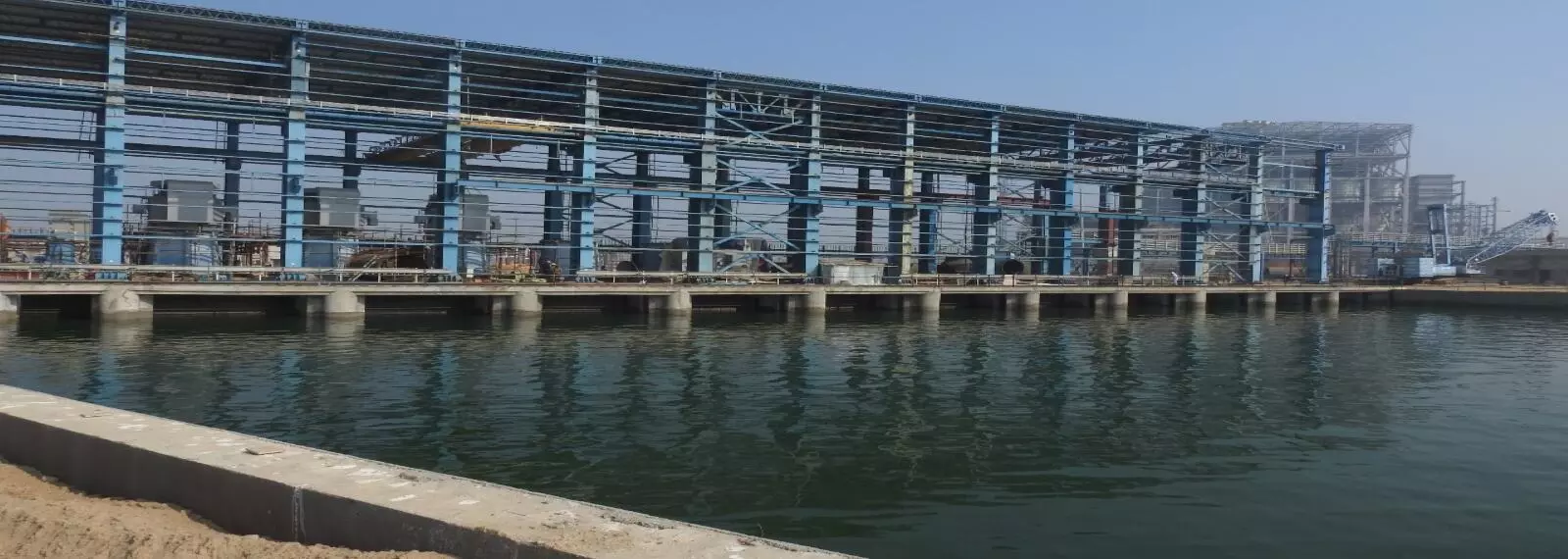
Neyveli Uttar Pradesh Power Limited (NUPPL), a joint venture between NLC India Ltd and Uttar Pradesh Rajya Vidyut Utpadan Nigam Ltd, has reached a significant milestone in the construction of the Coal-based Supercritical Thermal Power Plant in Ghatampur Tehsil, Uttar Pradesh. Unit-1 of this ambitious project has been successfully synchronised with the 765 KV grid.
This successful synchronisation marks a crucial step forward in NUPPL's journey toward the Commercial Operation Declaration (COD). The achievement underlines NUPPL's commitment to delivering reliable and sustainable power generation for the nation.
Prasanna Kumar Motupalli, CMD, NLC India Ltd, and Chairman, NUPPL, said, "I extend my heartfelt congratulations to the entire team at NUPPL for their dedication and hard work in achieving this significant milestone. We are proud of the progress made and remain committed to delivering efficient power to the people of India.”
NUPPL thermal power plant is now preparing for the next milestone of coal firing, which will pave the way for the much-anticipated COD. The entire power of 1,980 MW of NUPPL thermal power plant has already been tied up with the States of Uttar Pradesh and Assam, and Power Purchase Agreements (PPA) are in place.
In addition to the power plant, NUPPL is also making strides in the development of the linked coal mine, Pachwara South Coal Block in Dumka District, Jharkhand, which will provide a sustainable source of fuel for the end-use power plant. The 1,980-MW supercritical thermal power plant’s main boiler package is being executed by L&T, the turbine package by GE, and Balance of Plant (BoP) package by BGR.
NUPPL's commitment to environmental sustainability is exemplified by the plant's state-of-the-art design, featuring supercritical boiler and turbine-generator sets, along with adherence to the latest environmental standards through the implementation of FGD (Flue Gas Desulphurization) and SCR (Selective Catalytic Reduction) technologies, ensuring Zero Liquid Discharge.